When firms can count robots and cobots as capacity in the same way as they can count drivers and seated trucks, it’s a recipe for more implementation.
Old movies that imagine what the future could be like in 2020 or 2021 might involve flying cars or robots infused with artificial intelligence that can handle mundane tasks of vacuuming and even driving to the supermarket.
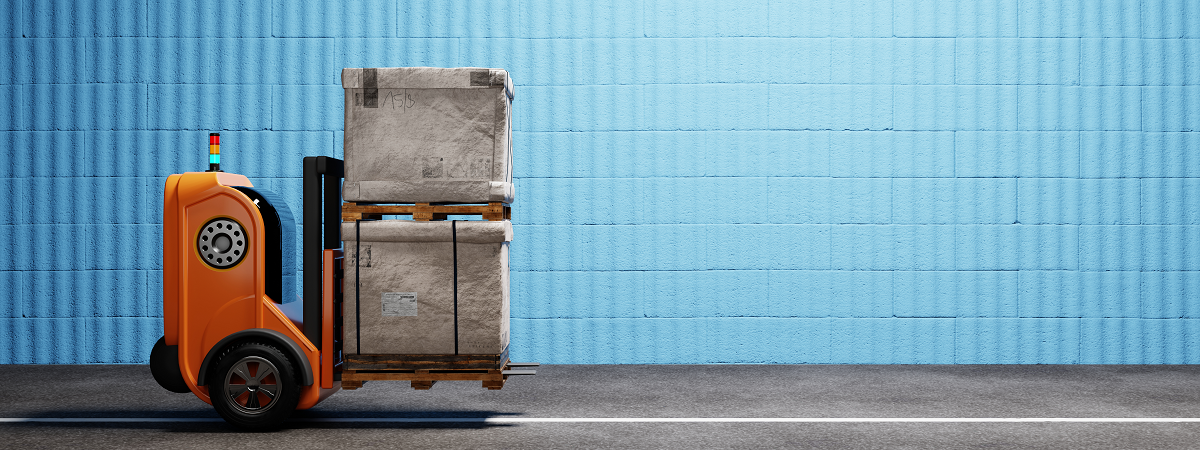
That technology does exist today, but it is in its relative infancy. That status, however, saw a growth spurt in 2020. The pandemic catapulted trucking and logistics into the future, speeding up the usage of robots; their cousins, the collaborative robots, or cobots; and automated transport vehicles, according to Çetin Meriçli, the co-founder and CEO of Locomation, an company that makes platooning technology.
Just how much further ahead trucking and logistics were pushed was evident in XPO Logistics’ Q4 and 2020 reports. XPO officials said the carrier shipped roughly five times more units using robotic technology in 2020 than it did in 2019. More than 25% of e-commerce volume in North America used advanced automation — including robots and cobots.
“In ways, the pandemic beamed us into the future,” said Meriçli.
Trucking and logistics companies — and shippers, too — discovered as the pandemic arrived last year that the supply chain was much more “brittle” than they thought, Meriçli said. Shortages of certain items became commonplace. Consumers, working from home, used e-commerce to drive up volume.
The lessons learned during the pandemic toughened up the supply chain, Meriçli said. The pandemic forced trucking, shippers and providers of third-party logistics to implement new technologies quicker and faster. To Meriçli, that was a good thing, especially for trucking.
“Trucking is the part where we need the most disruption,” said Meriçli.
As autonomous trucks arrive in the next decade, they will find their robotic cousins have been busy at work inside service centers and shipper facilities for years. The disruption in trucking is indeed happening, though at a slower clip.
“The pandemic emphasized the problems in trucking,” said Meriçli. “This is something that the industry has to react to now ... All prudent players are beginning to think about automation now to be able to move fast when the technology is [commercially] ready.” Meriçli would not name his clients, but in September, Locomation booked its first orders when Wilson Logistics went public with the news. Wilson ordered Locomation’s Autonomous Relay Convoy technology to be equipped on a minimum of 1,120 of Wilson’s tractors, with the first units delivered in early 2022.
In the next decade or two, the automated trucking landscape will be divided up in different uses, Meriçli said. Some trucks will be “drone followers,” convoying with a human-driven truck in the front. Some will be part of an entirely automated convoy. And perhaps some will drive solo, fully autonomous, but only on highways.
The biggest change could be what Meriçli calls “door-to-door” autonomy, when a robotic truck delivers from the shipper to the door of the customer, using even the surface streets.
Mr. Coboto
Firms such as Locomation work on such complete autonomy, what Meriçli calls the “holy grail” of the trucking future — Level 4 autonomy. Meriçli said in a decade, he expects tens of thousands of tractors to have Locomation equipment in the various tasks from platooning to drone following.
But in the meantime, it’s possible to step up the automation inside the service centers and operation locations at a faster rate.
Meriçli said the pandemic put pressure on the supply chain as never before. This new problem transformed the internal workings of LTL service centers and other operation centers much the same way the driver shortage has put pressure on carriers to find solutions such as automation, Meriçli said.
Thus, large LTL carriers have begun the process of enhancing their service centers for the robotic future.
At XPO, getting an assist from cobots in picking inventory is necessary to ensure its supply chain is efficient, company officials said.
“Supply chains are becoming more complex and fulfillment times are compressing, particularly in the direct-to-consumer space,” said Mario Harik, XPO’s chief information officer. “The most cost-effective way to meet the majority of customer requirements is by integrating advanced automation and intelligent machines into our logistics operations — robots, cobots, automated sortation systems and goods-to-person systems.” Harik said some of the systems can improve logistics productivity by four to six times. And “cobots deliver twice the productivity on average, working alongside our employees,” Harik said. “We’re seeing a substantial benefit to throughput from the implementations we did in 2019 and 2020.”
Dollars to bots
During the pandemic, logistics managers were perhaps better able to see the weaknesses in their supply chains and picking processes. Humans were tasked with handling surging volumes and more complex sorting-and-picking processes, all in an environment where the coronavirus was possibly present.
And one benefit to technology was it could work through a pandemic. Two research firms found the ability for companies to increase social-distancing measures within their facilities was the biggest benefit of automation during the pandemic. That research was released in mid-2020 by Honeywell and KRC Research conducted between April 21 and May 7.
The help technology offered became clear. Logistics companies, shippers and carriers began assigning more dollars to robots, AI, automation and cobots.
“Significant levels of budget have been moved toward automation,” said Deryk Powell, president of Velociti, a Missouri firm that helps companies deploy technology and assists in project management. “We are seeing the energy around the companies wanting to push this forward faster.”
Velociti helps companies retro-fit existing machinery —“sometimes thousands” of machines, Powell said — and tests the functionality of automation. Companies such as Velociti are involved in the automation of trucks, too, but the progress in that area is slower.
“It’s early,” said Powell. “We are involved with a few autonomy providers, very much in retrofit positions.”
Powell said he is not surprised by the accelerating robotic and automated progress — now. But that’s with the knowledge of what the pandemic and the business environment have done. Before the pandemic hit, Powell said he would have been surprised to see such progress.
“If you were to ask me nine or 10 months ago,” said Powell. “Absolutely.”
Meriçli said technology is helping carriers, shippers and 3PLs get more work done as assembly lines slow because of COVID-19, while demand increases. The coronavirus is also taking some drivers off the road, and it is slowing the process of training new drivers.
At licensing and testing bureaus, issuances of new CDLs have slowed, all while carriers struggle to find enough drivers. When firms can count robots and cobots as capacity in the same way as they can count drivers and seated trucks, it’s a recipe for more implementation.
Meriçli said he doesn’t fear a “digital divide” forming in the future, with some well-funded carriers having the best automation tech and others having less automation.
“Over time, we will see wider adoption,” said Meriçli. “We believe the smaller carriers can move faster, are more agile, are able to use the technology faster ... Because they can make decisions fast and adapt their processes to technology faster.”
Meriçli said the ultimate vision is complete automation, from service centers to carrier delivery. It will take time for such complete implementation, he said, starting with the problem areas of the supply chain.
“Everybody is looking at more dependable capacity,” said Meriçli. “Now is the time to begin re-engineering the supply chain.”
Originally appeared in Transport Dive. Written by Jim Stinson, Senior Reporter March 2, 2021.